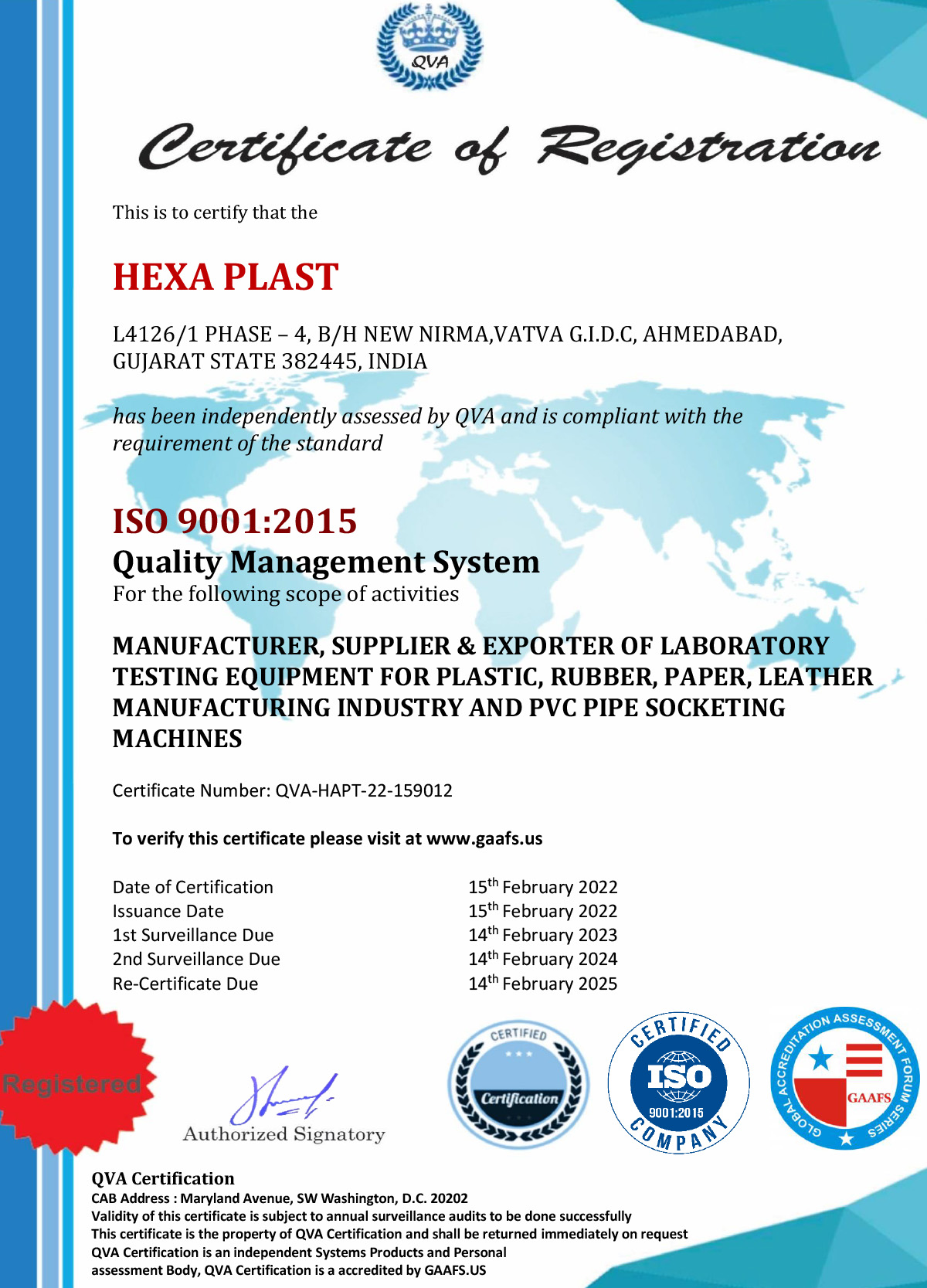
Quality Policy
HEXA PLAST TM is fully committed to being the leading provider of world class Lab Testing Equipment’s (Plastic Testing Equipment’s) by implementing latest inventions in electro-mechanical engineering.
Our primary goal is to achieve the highest standards of quality in all business units’ practices and operations without compromises. We will continually improve our company performance, while offering our customers a safe, cost effective and professional service to remain current and competitive.
“Quality Product is never been cheap & cheap is never been Quality Product”
1. Quality Planning
-
- Define quality objectives and specifications for the testing equipment.
- Establish quality standards and criteria for each product.
- Develop a quality control plan outlining inspection and testing processes.
2. Product Design and Development:
-
- Design testing equipment with quality in mind.
- Utilize advanced design tools and software for accuracy.
- Conduct design reviews and simulations to identify potential issues.
3. Supplier Qualification:
-
- Evaluate and select reliable suppliers for raw materials and components.
- Ensure that suppliers meet quality standards and certifications.
4. Incoming Material Inspection:
-
- Inspect incoming materials for compliance with specifications.
- Reject or quarantine materials that do not meet quality standards.
5. Production Process Control:
-
- Implement strict process controls and monitoring.
- Use statistical process control (SPC) techniques to ensure consistency.
- Train and educate production staff on quality standards.
6. In-Process Inspection:
-
- Conduct inspections at various stages of production.
- Identify and rectify any defects or deviations from standards.
7. Testing and Validation:
-
- Perform rigorous testing of the testing equipment to ensure functionality.
- Validate equipment performance against design specifications.
- Use various testing methods, including destructive and non-destructive tests.
8. Document Control:
-
- Maintain comprehensive records of all quality-related activities.
- Ensure documentation is up-to-date and easily accessible.
9. Final Inspection and Testing:
-
- Conduct final inspections to verify product quality.
- Perform functional tests to ensure equipment meets its intended purpose.
10. Packaging and Shipping:
-
- Ensure proper packaging to prevent damage during transit.
- Confirm that the shipped products match quality standards.
11. Customer Feedback
-
- Collect and analyse customer feedback.
- Implement corrective actions based on feedback and quality data.
- Continuously improve processes and products.
12. Quality Audits:
-
- Conduct regular internal audits to ensure adherence to quality processes.
- Engage in external audits if necessary to maintain certifications.
13. Certifications and Compliance:
-
- Ensure that products meet industry-specific standards and regulations.
- Obtain relevant certifications as needed.
14. Recall and Corrective Actions:
-
- Develop a recall plan in case of product defects or safety concerns.
- Take swift corrective actions and notify affected customers when necessary.
15. Training and Development:
-
- Provide ongoing training to employees to enhance their skills and knowledge
- Foster a culture of quality and continuous improvement.
16. Customer Support:
-
- Offer excellent customer support to address any quality-related issues or inquiries.
- Provide warranty and after-sales services as appropriate.